|
Many production processes involve dispensing a certain
amount of fluid, either as an ingredient to be mixed with other ingredients
to make a batch of product, or as a dose injected into a product stream, or
as the end product itself to fill containers for shipping. Often, a PLC is
used as the overall process control. The PLC may be controlling a half dozen
steps in the process, but it should not be directly controlling the
dispensing step. The Eclipse batch control is a better way. The Eclipse and
the PLC can work as a team, with the end results of better system
performance and lower cost for the controls.
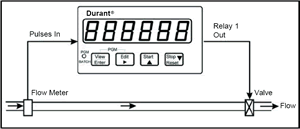
Unlimited potential for any batch dispensing system in
a variety of industries:
-
Liquid filling machinery
-
Mixing machinery
-
Concrete batching
-
Waste water treatment and water purification
|
|
A bit more detail: In its simplest form, a closed-loop
batch dispensing system consists of :
-
A flow sensor (flowmeter), which sends an electrical
signal proportional to flow rate to the
-
Batch control, which accumulates the amount of fluid
that went through the pipe, and opens and closes the
-
Solenoid valve.
In operation, the process or machine operator enters a
preset number of gallons, or liters, or pounds, etc. into the batch control,
and presses the start key on the control. The control energizes an internal
relay, which opens the valve, and flow commences. The batch control then
counts out the amount of fluid that has been dispensed until it reaches the
preset amount, at which time it de-energizes its relay, which closes the
valve. At any time during the batch delivery, the operator should be able to
press the stop key on the batch control, causing the relay to de-energize
and stop the delivery. The operator can then either resume batch delivery
from the point where it had been stopped, or reset the batch by using keys
on the control.
If the PLC controlling the overall process must also
perform the batch control function, several things must be considered.
First, no flowmeter produces a raw output signal that is compatible with a
PLC. A signal conditioning device, such as a flow transmitter, will be
necessary to convert the flow signal into something the PLC can read. Flow
transmitters can add significant cost to the project. Second, a compatible
transmitter output would normally be a 4-20 mA signal, which means that the
PLC must have an analog input. Add a few more bucks. Third, how does the
operator enter a batch preset into a PLC? Add the cost of an HMI or register
access module to the project. Finally, Start and Stop pushbuttons must be
added to allow the operator to control the delivery.
Our solution: Use an Eclipse as the batch control.
Since it can accept the raw signal from most flowmeters, no flow transmitter
is necessary. The Eclipse can either control the valve directly, or provide
a relay input to the PLC, so no analog PLC input is required. The Eclipse is
the operator interface, providing count and rate displays and preset entry
on its front panel. Finally, there is no need for the Start and Stop
pushbuttons; they are included on the Eclipse front panel. Beyond the cost
savings, the Eclipse can control the delivery with no scan time variation,
and it provides an operator readout of flow rate and total, things the PLC
cannot do. |
|